Failed Tanking and Broken Business Models
This article chronicles our experiences in remedying failed habitable/converted basements, where cementitious slurry tanking has been installed by non-specialist Contractors, who have been provided with minimal training by materials suppliers. Those suppliers will offer to write specifications for the job, and the contractor can then install. It's a difficult system to get right and these examples are testament to that.
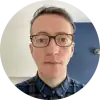
By James Hockey
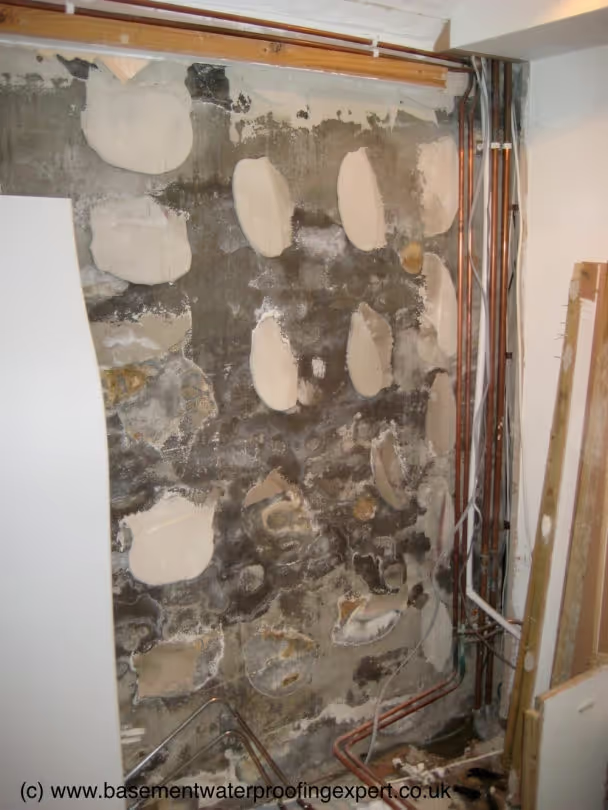
At present we are completing a remedial waterproofing scheme within a residential basement, where we are installing cavity drainage waterproofing to address issues of penetration past the internal cementitious slurry tanking system.
Nothing particularly unusual about that, but it is significant to me at least, in that this takes our turnover remedying failures in that specific slurry tanking product, to over £250k excluding VAT.
Must be a terrible product??
No not at all, it is a polymer modified cementitious tanking slurry and we use these regularly, albeit typically as a detailing product or as part of a combined waterproofing system, rather than as a standalone waterproofing system in its own right.
While we may use a polymer modified slurry system from a different supplier, there is no technical reason why I would not use the product referred to above.
This is because the technology is essentially the same, slurry systems are thin (1-3mm) barrier coatings comprising graded aggregates, cements and chemicals. The polymer additive grants a degree of flexibility and enhanced bonding characteristics.
Thankfully, products will generally perform to specification (this product will resist a hydrostatic head of X metres etc. etc.), just as the manufacturers say they will, because of quality control typical in the manufacturing process.
Why therefore has so much been spent on remedial work to address failed installations of this particular cementitious slurry?
This is because in most cases it is not product failure; it is associated with the fact that waterproofing systems must be designed and installed correctly in order to function correctly.
This might sound simple, but if we take internal cementitious tanking as a relevant example, this form of waterproofing seeks to provide protection by forming a physical barrier to exclude / block water out of a basement space, so that a dry internal environment is created.
In order for this to be achieved, that barrier must be 'perfect', i.e. free of holes/defects, because like with any liquid holding 'tank', it will not hold or exclude water if it has holes in it.
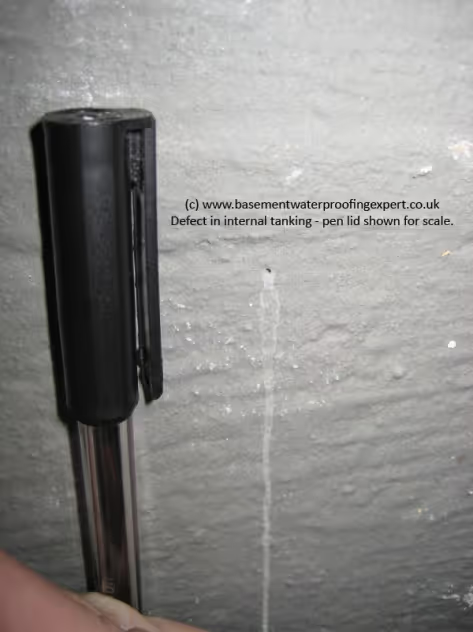
In addition, where such barriers are applied to the internal face of a structure, water in the ground externally moving through that structure (from the outside in) will essentially bear upon the tanking at the internal face, applying a pressure which seeks to push the tanking away from the substrate upon which it is applied.
Because of this, the method is entirely reliant on the bond that is formed between the tanking product and the substrate upon which it is applied.
This means that the substrate must be suitably prepared (to provide a 'key') in order to receive the tanking. This takes a great deal of care, attention and understanding in the installation.
The structure itself must also be capable of absorbing the loads applied to it by hydrostatic pressure, because once you tank that structure, it is the structure (to which the barrier tanking has been bonded) that has to support the weight of water bearing against it.
In short there is a lot to consider and hence the requirement for care and attention.
Lets look at some examples where this was lacking:
In this example a render base-coat was applied over masonry, to provide a level substrate to receive the polymer slurry tanking system. Not unusual, however the surface preparation, render specification and installation was totally incorrect with this resulting in water ingress, remedied by full strip out and replacement with internal cavity drainage waterproofing (click the first photo to browse through). Homeowner had a guarantee certificate signed by installer (no longer trading) and product manufacturer, who said they don't guarantee workmanship (this without having even inspected), leaving the homeowner to remedy.
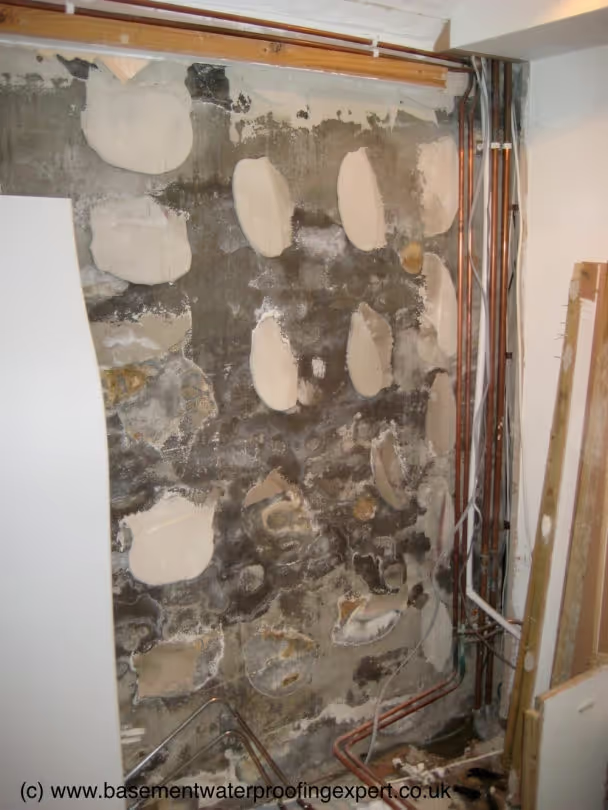
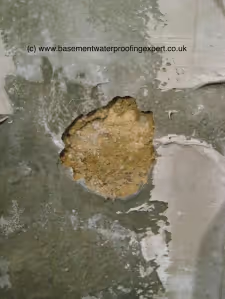
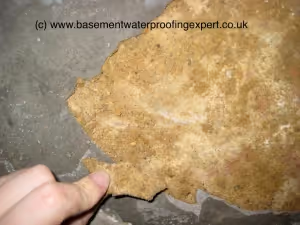
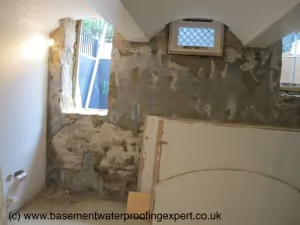
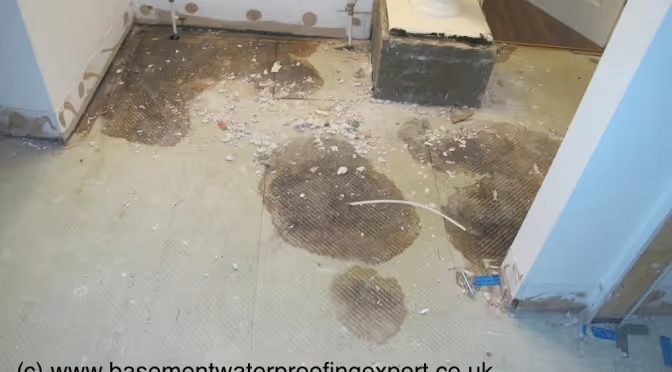
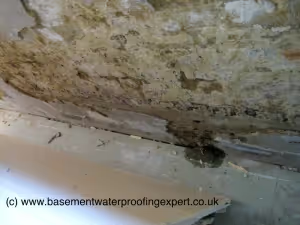
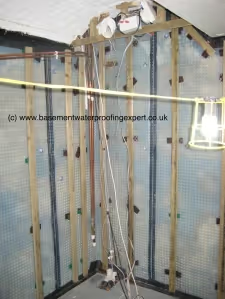
A different property now, this one had screed laid over a cementitious multi-coat render system. Water came past the render and caused the screed to heave and crack:
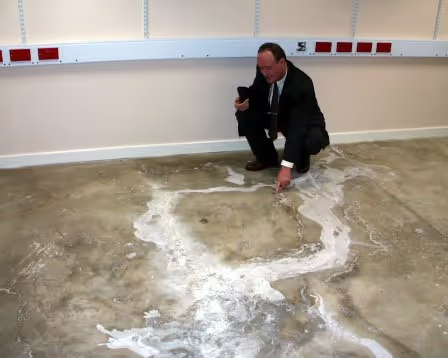
Render applied over weak brick substrate, the face of the brick de-laminates / comes away with the render:
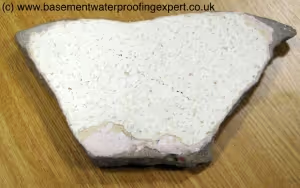
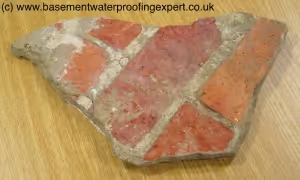
This (below) is an example of not considering the nature of the structure, the cellar flooded severely and the installer decided that cementitious tanking was the answer. As a result tanking was applied over the existing floor construction (thin layer of concrete over the original historic floor) and when the ground filled with water resulting in hydrostatic pressure, the floor went into floatation resulting in differential movement (cracking) at the wall floor junction. Once the tanking cracks, water can obviously penetrate.
So, a repair was attempted by installing a flexible product at the wall floor junction (white putty-like material), but this did not have the desired affect and the space flooded again. We remedied by adding drainage channels and a reliable sump pump system.
.avif)
Not cementitious tanking, but a good example of the forces involved where hydrostatic pressure comes to bear. In this case a bitumen sheet membrane has been applied to the internal face of a retaining wall within a cavity. Bitumen membranes remain malleable and so when pressure came to bear, the membrane 'bowed' in, and pushed over the inner block leaf which was not tied back (so as not to perforate the membrane)

Another classic industry example of hydrostatic pressure, in this case causing a floor slab to fail spectacularly:
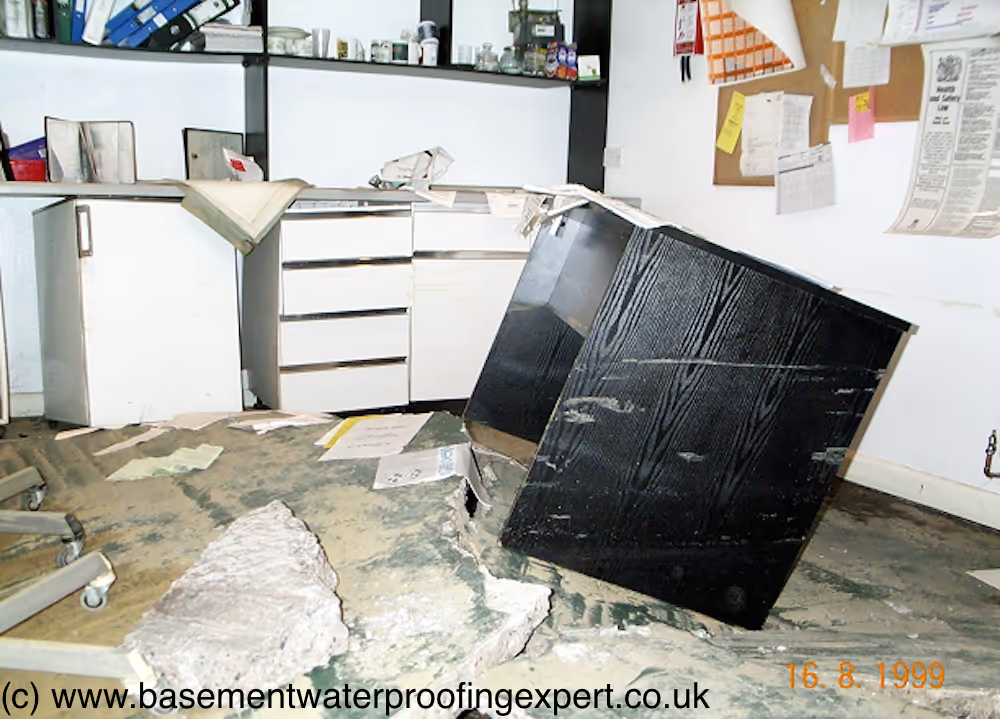
I hope that the above illustrates the that the design for a tanking system must be right in the first instance, and the installation has to be meticulous. If not then expect problems in the event of groundwater pressure coming to bear.
As an example of the way in which this work should be approached, we are at present tanking an existing basement swimming pool which is circa six metres below ground. We've had the tiles hacked off and then the structure has been grit blasted with glass beads, and we've then had staff working in there for the last two weeks with diamond plate grinders going over the structure to abrade and/or cut out any details, which will then be patch repaired using primers and epoxy mortars, so we can ensure no issue with the proposed tanking system.
Once that's finished the substrates will be cleaned using an industrial three motor vacuum powerful enough to destroy any carpet. We'll look to achieve a very clean and sound substrate before we consider applying any tanking.
In respect of the business model I refer to in the title of this post, the £250k+ remedial works undertaken, have as far as I know, all been in structures which have been tanked by non-specialist contractors.
This isn't necessarily to say that all non-specialists are incapable of undertaking this work, and to be fair I've just looked at a problem with the exact same product/system installed by a damp proofing firm, but it does make me question the validity of this approach, particularly where homeowners or insurers end up having to spend out on remedial systems when these companies do not honour guarantees or cease trading, which is not uncommon.
The specific business model seems to be to attend site and specify the works, then selling the materials for installation by a general contractor that has had some limited degree of training so gains 'approved' status, it then goes to site and schoolboy errors are made.
My opinion is that part of the reason for such failures is a combination of the difficulty in making a cementitious tanking system function as intended, combined with installation by operatives with no or very limited understanding - probably the main element in what causes failures.
I am also of the opinion that the manufacturer/suppliers should bear some of the responsibility for the financial cost and distress caused to homeowners where these systems fail, because they seemingly promote work by non-specialist contractors on the basis that the work is not rocket science.
If it was treated like a scientific endeavour, maybe there wouldn't be such issues.
I also think that these issues start with poor management, i.e. those running the installation firm do not ensure that site staff are adequately trained or informed of what is required, and the site guys who generally are conditioned to work quickly, charge in and get the job done but incorrectly and without the required attention to detail.
I do actually sympathise with the contractors that install these systems because no doubt the projects are entered into with the best of intentions, but perhaps without the appreciation of what is required, and with false confidence garnered via limited training?
Call me biased because all said and done I am a specialist waterproofing contractor, but I/we specialise in dealing with problem basements and you reach a point fairly quickly where you can recognise what is wrong with this practice.
For all I know it may be a small number of systems which fail, but what is your tolerance for this, when these issues often cost tens of thousands of pounds to sort out? One job, ten? It should be zero.
Rather than having waterproofing work designed by suppliers that won't accept design responsibility (provide guidance only), then with installation by staff that may only install waterproofing once in a blue moon, does it not make more sense to have design and installation responsibility under one roof with installation by staff that install day in day out? What about using firms that provide long terms guarantees day in day out and have the history to back this up?