Deck & Flat Roof Waterproofing Contractor
Get in touch
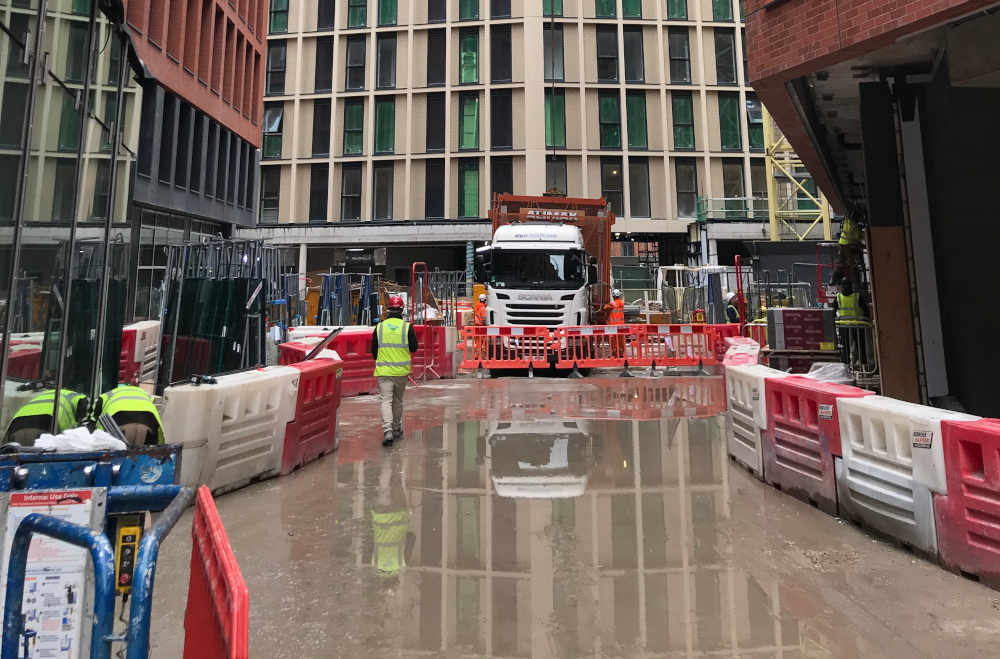
Trace Basements are specialist deck waterproofing contractors.
'Podium decks, buried roofs, green roofs, blue roofs, flat roofs with continuously supported coverings' – these are the terms used to describe waterproofing systems which are ‘flat’ or rather laid to minimal falls, typically including some form of build-up over (paving for example), which conceals the waterproofing.
These structures can be common above basements, where basements extend out beyond the exterior walls of the building above ground.
Podium Deck, Buried Roof & Flat Roof Waterproofing
Partnership with AXTER
The design and installation of systems which protect against rainwater ingress from above, is its own specialist field, with specific differences when compared to waterproofing for below ground structures. It is closer to roofing, than it is to basement waterproofing.
Further to this, Trace are pleased to partner with AXTER, a flat roofing specialist manufacturer, providing design, quality assurance, guarantee, insurance and training support, alongside our own design and installation expertise.
Trace Basements, as an approved Axtershield installer, are trained and certified to install two Axter material systems, providing flexibility across differing project scenarios.
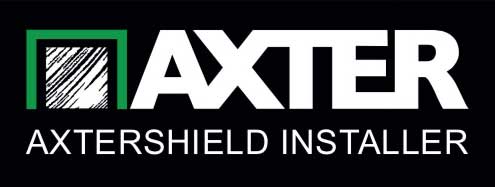
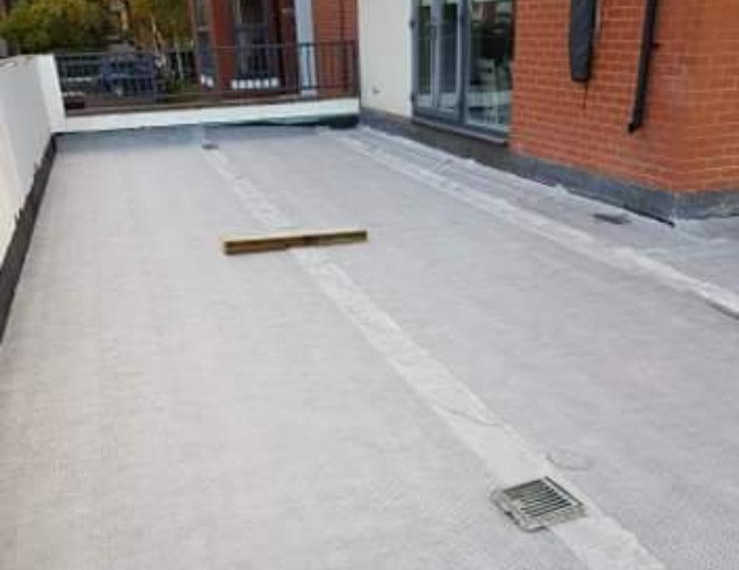
Image is of a Polyurea deck waterproofing application to a 1,200m2 podium deck.
Specialist Expertise
Our team possesses specific knowledge in deck waterproofing systems, understanding the unique challenges of protecting structures from above-ground water ingress
Manufacturer Partnership
Direct collaboration with AXTER ensures access to premium materials, extended warranties, and ongoing technical support throughout the project lifecycle
Long-term Performance
We prioritise durable solutions with extended material warranties, eliminating concerns about system failure beyond standard warranty periods.
Comprehensive Protection for Deck Structures
Axter Starcoat PMMA
PMMA (polymethyl methacrylate) represents a cold-applied, four-layer reinforced liquid waterproofing system. This flexible solution proves particularly effective for smaller areas, complex detailing work, and applications requiring UV-stable materials. The system is available with manufacturer warranties of up to 25 years.Axter Wilotekt PlusAxter Wilotekt is a second-generation hot melt waterproofing system engineered for larger applications and installation beneath various build-up configurations, including green roof systems. The primary advantage of Wilotekt lies in its exceptional durability and longevity, backed by manufacturer warranties of up to 35 years and a life-of-structure expectancy of 60 years.For buried and inaccessible waterproofing applications, material longevity becomes paramount. Clients require confidence that their investment will perform throughout the building's operational life, particularly when access for maintenance or replacement is severely limited. Wilotekt provides this assurance where many alternative materials offer only ten-year warranty periods.
Falls and drainage are important aspects of deck waterproofing
Decks will always receive rainfall and management of that water is a key consideration. What you do not want is for water to collect, stand and pressure - it is hydrostatic pressure which forces water through any defects/pathways present, and long term standing water can be detrimental to some materials.
What we've seen in the past is no falls, and no drainage, or that the drainage outlets are installed at the level of the finishes (such as paving), and are too high to receive water at the level of the waterproofing. This is how you create a reservoir above the waterproofing, not what we want.
Decks should achieve falls of 1:80 in their permanent loaded condition to outlets which can receive water draining off of the waterproofing
Quality assurance methods for deck waterproofing materials
Trace employ forms of deck waterproofing which can be tested via what is know as spark or holiday testing. An electrical current is passed over the membrane via specialist equipment which identifies if there is any loss or conduction of the current through the waterproof material, i.e. is there a hole or thin section weak point, representing a risk to the system. This is undertaken by a third party and is an important measure in ensuring the quality of the installed waterproofing system.
Permanent leak detection systems for decks
These are systems which are installed in association with the waterproofing system, with the principle being that in the event of any issue, it is possible to locate the area in which water is bypassing a membrane. Deck structures inevitably include multiple layers of material (for example - insulation), through which water can track laterally meaning that where you see water internally, may not match the location of a defect in the waterproofing. Such systems are in their infancy in the UK waterproofing market, and the focus is always on design, installation, materials and QA, such that defects are avoided.
Nevertheless, it is the norm in basement waterproofing for Designers to consider risk of defects and strategy for repair, (both key points in BS8102 Protection of below ground structures against water) and we note that some of latest design guides produced (we have been involved in editing the PCA guidance doc. ourselves) advise the same requirements in respect of repairability. Further to this we expect that these systems will become the norm, particularly where decoupled waterproofing systems are employed.
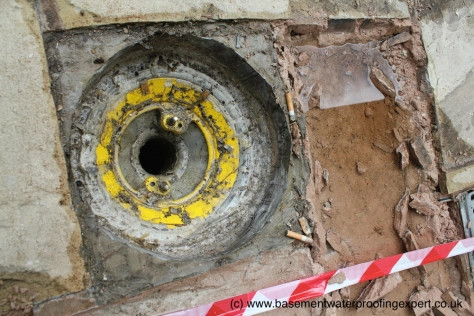
What a state, standing water in bedding materials next to a drainage outlet, yet the water cannot drain into the outlet which is too high and can only receive water at finishes level, NOT the level of the waterproofing.
Experts in Structural Waterproofing & Timber Repair
Trace are Industry leading waterproofing contractors
Get in touch
Winning awards & Accreditations
.webp)
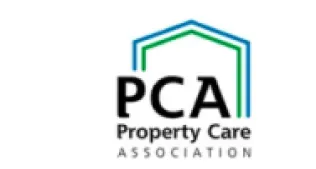
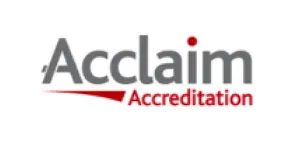
.webp)

Experts in Structural Timber Repair for Listed Buildings
Complex buildings need the highest level of expertise. We specialise in dealing with complex issues of moisture in buildings, including basement waterproofing, waterproofing maintenance, timber repair for new and old buildings.
Find out more
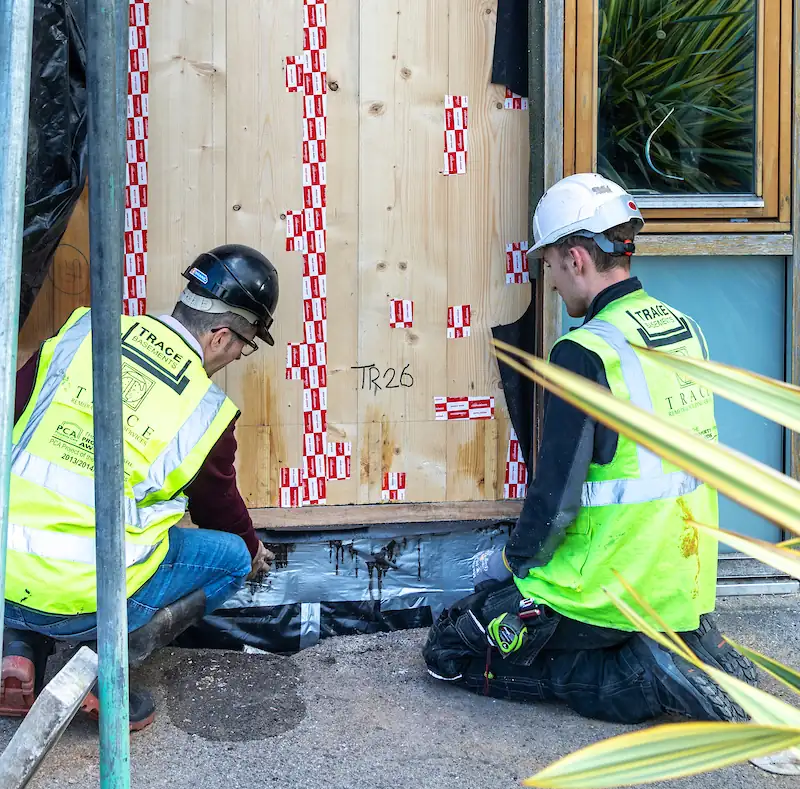