Slurry Tanking Systems, Explained and Reviewed
Slurry tanking systems, what are they, how do they work, is it effective? We answer these questions and more.
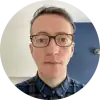
By James Hockey
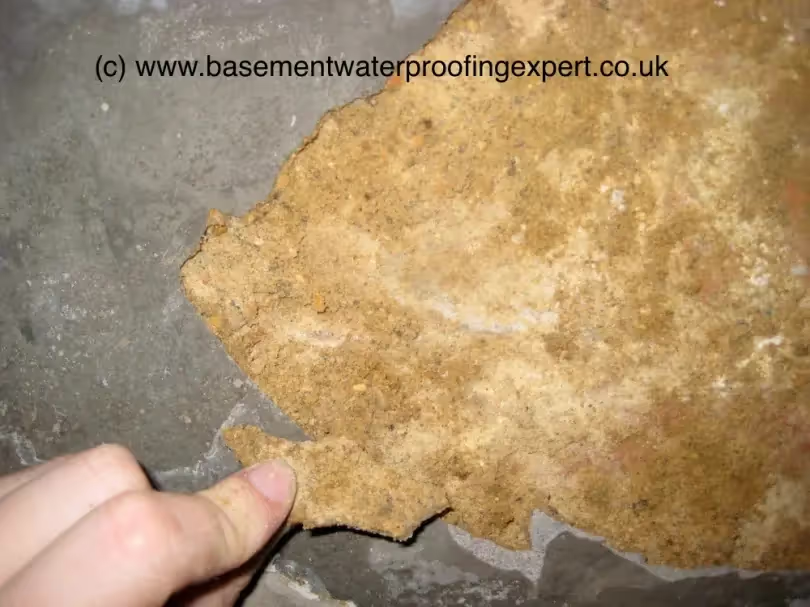
Slurry Tanking Technology
Slurry tanking is a cementitious (cement based) coating, which is bonded to a structure to provide a physical barrier to block water out. It is 'Type A Tanked Protection' as defined by BS8102 Protection of below ground structures against water ingress.
It is mixed to a liquid creamy consistency, and applied usually by brush in 1-2 coats, to provide a circa 2mm thick waterproof layer.
These materials are comprised of ordinary portland cement (OPC), graded aggregates (graded meaning that the particle size is controlled), and chemicals - so they say.
It is worth noting that the cement you buy bagged from a builders merchants is typically cem-2, so up to 65% OPC and the rest cement replacements. It is likely that the OPC in slurry materials is comparatively pure, and I would anticipate that it is the OPC and graded aggregates (sands) that do much of the work in providing a barrier to water.
OPC content in bagged cement explained by the Concrete Society.
How so? When water is added to cement, a paste is formed which coats the aggregate particles. During curing and in the presence of water a chemical reaction occurs whereby crystals grow from the paste, intertwining and locking together the particles of aggregate. With the right blend of these materials, and subject to proper curing, an impermeable material can be created.
Types of Slurry Tanking
Properties of slurry materials can be significantly influenced by what they are mixed with. Typically slurries will be mixed with clean water, or a liquid polymer.
Water produces a rigid coating, which is comparatively vapour diffuse.
By contrast, mixing a slurry with a liquid polymer, can provide an elastic flexible membrane with lesser vapour permeability.
Slurry coatings may be un-reinforced, fibre reinforced or reinforced with plastic meshes and tapes.
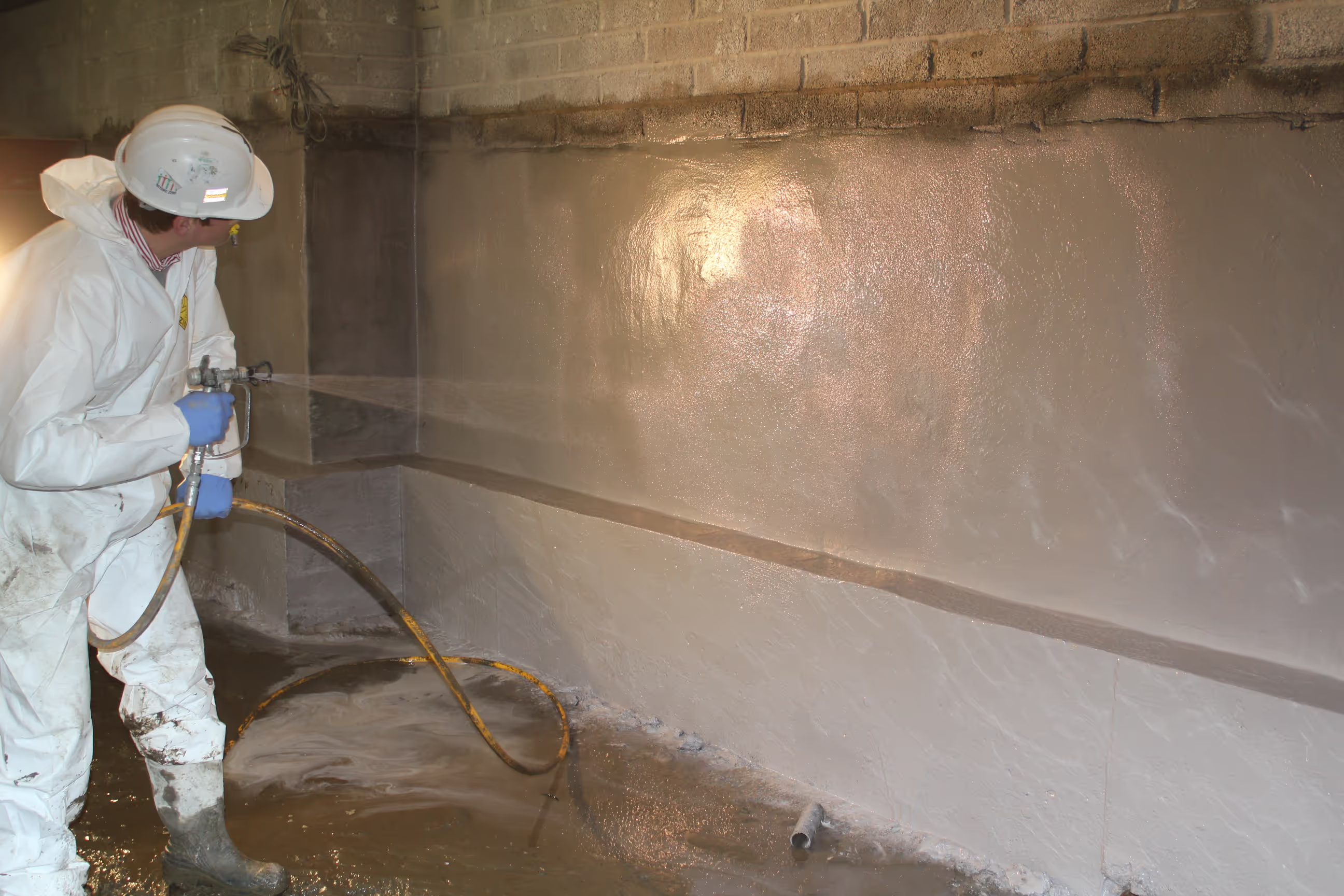
Practical implications of slurry tanking systems
In theory a polymer modified slurry can accommodate some degree of flexural movement and cracking, whereas a slurry mixed with water is unlikely to be able to do so. You might assume that structures do not move, but they can and do. In basements, walls and floors can be subjected to soil and hydrostatic pressure, which can induce movement. We do also tend to see cracks propagate around structural members supporting a load from above, as if that load induces movement. Settlement or 'creep' in structures is a known phenomenon.
So a polymer modified / polymer rich slurry is the answer surely? Our experience is that such materials are particularly sensitive to moisture, as in application to wet walls, can cause the polymer to leach out of the slurry, which is no good. The extent of movement that can be accommodated, especially in an unreinforced material, is limited.
So, treating a new concrete structure with polymer slurry as a preventative measure, workable. Treating joints in concrete outside in November, or a wet wall internally, better in our experience to use a slurry mixed with water. If there is ongoing water ingress, this would have to be stemmed with waterplug materials prior to application of the slurry.
Slurry System Design and Installation
To achieve a successful outcome, we do have to understand the materials, and have the right materials, but we also have to understand how to install these and how they will interact with the structure, with the examples above (how wet) being one such example.
Others considerations with slurry systems are
Substrates
Flat and level (ideal) or convoluted? In some cases for the latter, smoothing render coats might be applied first, this adds another layer which can be a potential mode of failure if not correctly formed (mix and curing).
Substrate preparation
Probably the most typical mode of failure, application to the internal face of a wall is referred to as waterproofing of the negative face, because water pressure moves through the wall and the pressure pushes the barrier away from the substrate. Hence preparing the substrate to achieve a good 'key' and using bonding agents to enhance bond, are considerations.
Structure
Slurry is not a structure in of itself, it is reliant on the structure to absorb loads applied by hydrostatic pressure, and so the nature of the structure should be assessed.
Note that because of the requirement for adhesion, such materials are not 'reversible' and not considered appropriate in buildings of historic significance.
Defects in Slurry Tanking, Strategy for Repair and Testing
All should be considered, but often isn't.
Slurry tanking system summary
Slurry materials are great, but to be completely transparent, we don't use them as systems in their own right, as a tanking system in isolation. We tend to use them as detailing products (such as tanking locally over joints in underpinning), or as a method to slow down the rate of ingress, we don't assume we'll completely stop it.
With everything we know (20+ years of focus on learning and structural waterproofing), we know it's a method of waterproofing requiring careful attention to detail and understanding. That it can be purchased over the counter in builders merchants for use by those that don't understand waterproofing, is in some respects, astounding.
(This article on slurry system failures may aid in illustrating this - link to Trace slurry blog post)
We hope that this aids in your understanding of these materials and particularly the level of consideration associated with them, which is often underappreciated.
A bit about Trace Basements
As per the link to our post just above (Failed tanking and broken business models), we have a lot of experience in dealing with failed tanking systems, but in understanding how they fail, we understand how not to fail, want to get in touch? See our contact page.