Sub-floor Voids, Timber Floors and Ventilation
Why do older properties often have suspended timber floors with sub-floor voids beneath? To understand this it is perhaps worth asking why all properties don’t just have solid concrete floors?
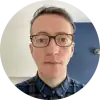
By James Hockey
.avif)
I'm not categorically sure, but my presumption is that prior to the availability of plastic DPM's, (polythene damp proof membranes) which are now placed beneath ground-bearing concrete slabs, it was not practical to lay these without them absorbing moisture from the earth beneath, resulting in a damp floor.
How therefore could those that came before us, create dry comfortable floors in an easy/practical fashion?
A suspended timber floor is just that - SUSPENDED, timber joists (beams) spanning (suspended) between walls, often also supported on a series of sleeper walls beneath, so the floor is lifted up out of the earth and therefore mostly away from moisture.
It is important that timber is maintained in a suitably dry condition. Timber is essentially dead organic material and will decay when sufficiently wet, just like when the leaves fall from the trees in Autumn, in time they decay.
So while we can see the sense in a suspended timber floor, there are still sources of moisture than can affect these. What are they?
Capillary moisture within substrates which the timber bears on and into, and the other is airborne water vapour.
.avif)
.avif)
Depending on the age of the property, floor joists may bear on/into masonry which resides above a physical damp proof course, intended to keep that masonry dry.
.avif)
In respect of vapour, this is an important consideration. There is vapour in the air all around us, but elevated vapour levels can occur within sub-floors - particularly where there are exposed earth oversites - as a result of evaporation from that earth and from damp walls below DPC level.
Wood is hygroscopic, which means that it can absorb moisture from the air. Because there is always moisture in the air, ‘air-dry’ timber will typically be anything up to circa 12% moisture content, i.e. it is not 100% dry/free of moisture.
When timber reaches a higher moisture content of 18-20%, there is risk of decay, so it is important to control vapour levels within sub-floor voids, so that timber is preserved and does not decay, requiring expensive and disruptive remedial works in time.
.avif)
This is where air-bricks come in. These are intended to ventilate a sub-floor void, so that vapour is maintained at a sufficiently low level, to keep the moisture content of the timber to a low enough level whereby decay does not occur.
An brick to a sub-floor is like an open window is in the house above, in that they can allow loss of vapour to the exterior through vapour drive (high internal vapour pressure seeking to equalise with lower external vapour pressure – see my previous posts to understand this), but also and perhaps more importantly where there are air-bricks on opposite sides of a building, they allow cross-flow ventilation, i.e. where the wind moves air through.
Ideally air-bricks will be present along a wall every approx. 1.6m. Old terracotta/clay air-bricks can also be swapped out with modern equivalents to improve air flow since the surface area of vent provided is greater with the modern fittings.
So what does this mean in practical terms if you’reinspecting or refurbing these buildings? Well air-bricks can often be concealed where external ground levels are raised by new driveways, block paving etc. or tenants in some cases will block these up to try and prevent draughts. You can easily see this when walking up to a property.
Bouncing on a suspended timber floor close to external walls can give you a feel for decayed bearing ends, if there is movement in it.
Where there are no floor coverings, it’s worth a look into any access hatches – look for signs of mould/fungus, can you see a physical DPC? Is there any standing water? If you have a moisture meter these can be used in the joints – look for readings > 18/20%.
.avif)
Just another factor in understanding how buildings work – hope that’s useful.
PS: Suspended floors are still commonly used in new construction, but typically pre-stressed reinforced concrete beams and blocks (beam and block), or with pre-cast hollow-core concrete planks (Bison-beam or similar).
PPS: Sub-floor voids where extending below external ground level, can be prone to flooding where the ground around the structure becomes saturated, in a similar fashion to basements and cellars, as some of these demonstrate.
.avif)
.avif)
.avif)