Top 5 Problems with Cavity Drainage Waterproofing Systems for Basements
Waterproofing systems are not 'one size fits all'. Is cavity drainage right for you? We look at some of the problems, and the solutions, associated with cavity drainage waterproofing systems.
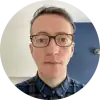
By James Hockey
.avif)
There's a maintenance requirement!
Just like with many other aspect of a property, cavity drainage waterproofing systems need to be adequately maintained. This is easily achieved with a well designed system (includes service ports) and a competent experienced Contractor that offers to maintain what they install. This will ensure that the system continues to function and protect long into the future, which is ideal but there is a cost (note that your contractor should advise you of what this cost will be upfront and in advance of undertaking any work).
Pumps use electricity!
Unlike other forms of waterproofing, the pumps that often (but not always) required to provide cavity drainage waterproofing system, require electrical supplies in order to function and protect. How much do they use then?
A 400w pump cycling an average of seven times a day at 10 seconds per cycle, equates to 3.1 kW hours across the course of a year. At an Oct 2022 average for the North West of England (where we're based) of 32.4p per kWh, it's just over a £1 spend.
For comparison a typical 55" LED TV running for 2-3 hours per day would equate to 103kWh or £33.37 per year. Therefore it's not a huge spend, particularly when we're often installing 250w pumps within these types of system, but there is a running cost.
The structure gets wet!
Cavity drainage collects and removes any water which penetrates through the structure, (and through any other barrier waterproofing system applied to that structure). This means that the structure is exposed to water / gets wet.
Let's consider this, if you have a brick or stone built structure, and there is water ingress, and alternatively we seek to block water out using a barrier based tanking material (not cavity drainage) applied internally, then everything beyond that internal barrier (the whole structure) remains damp/wet.
Even where we have something like an impermeable waterproof concrete structure, the joints between pours (sections of concrete) have to be sealed, which is commonly via 'waterstops' installed in the middle of the joint, between an inner and outer layer of steel reinforcement. The outer layer of steel reinforcement is therefore exposed to water. What will last longer in water? Brick or steel? Likely the former, yet Structural Engineers design concrete basements using such details constantly.
Point being, that every masonry (and concrete) built cellar in the land, sits into the earth, and with our climate that earth will always contain a degree of moisture.
The only way we can try and achieve a completely dry structure, is to build from new and put the barrier waterproofing on the outside. For habitable usage, this would be combined with cavity drainage, so if there is any ingress, it doesn't affect the interior, and then we're back to a position of water in the structure.
The lifespan of mineral based structural components such as brick, stone and concrete is not readily affected by the presence of ordinary groundwater.
It takes up space!
Cavity drainage membranes do take up some space. It's pretty minimal though and designers should consider the optimal design for your basement to negate any detrimental implication. A standard cavity drainage membrane applied to a wall is 8 millimetres deep, and to floors is either 8 or 20 millimetres. This is much less than plasterboard (12.5mm or 15mm with skim finish), insulation (50mm to 150mm), screed (30-65mm) or T&G timber floor boards (22mm). We can employ meshed membranes and dab fix boards where a minimal depth build up is required, or can combine with details employing alternative materials such as epoxy resins at 450 microns (0.5 milimetres).
It's a faff!
In order words is such difficulty or complexity necessary? Yes there is some complexity to cavity drainage waterproofing, but if you design it and install it all day every day, and get it right, in means dry basements. That is definitely not a problem.